The basic forming process of EPS involves preheating, mold closing, feeding, heating, cooling, and demolding.
Mature pre fired beads are heated by steam for about 20-60 seconds, during which pressure is generated after thermal expansion. At this time, the polymer is softened, and the sum of the pressure generated after the evaporation of the foaming agent and the pressure generated by the air in the bubble hole is greater than the external steam pressure. The beads expand again, and the gap between the beads expands to form a whole, forming a foam product with the same shape as the mold cavity, which is formed after cooling. After the product is formed, it requires post-processing such as dry cutting and demolding.
1. Preheating: The preheating temperature is generally around 100 ℃. The preheating time depends on the amount of metal in the mold cavity and the requirements of the product. The more metal there is, the longer the preheating time. Similarly, the thickness of the mold wall is the same. The automatic sheet metal factory reminds everyone that any project that increases the mold area or the number of model pieces must also extend the preheating time accordingly.
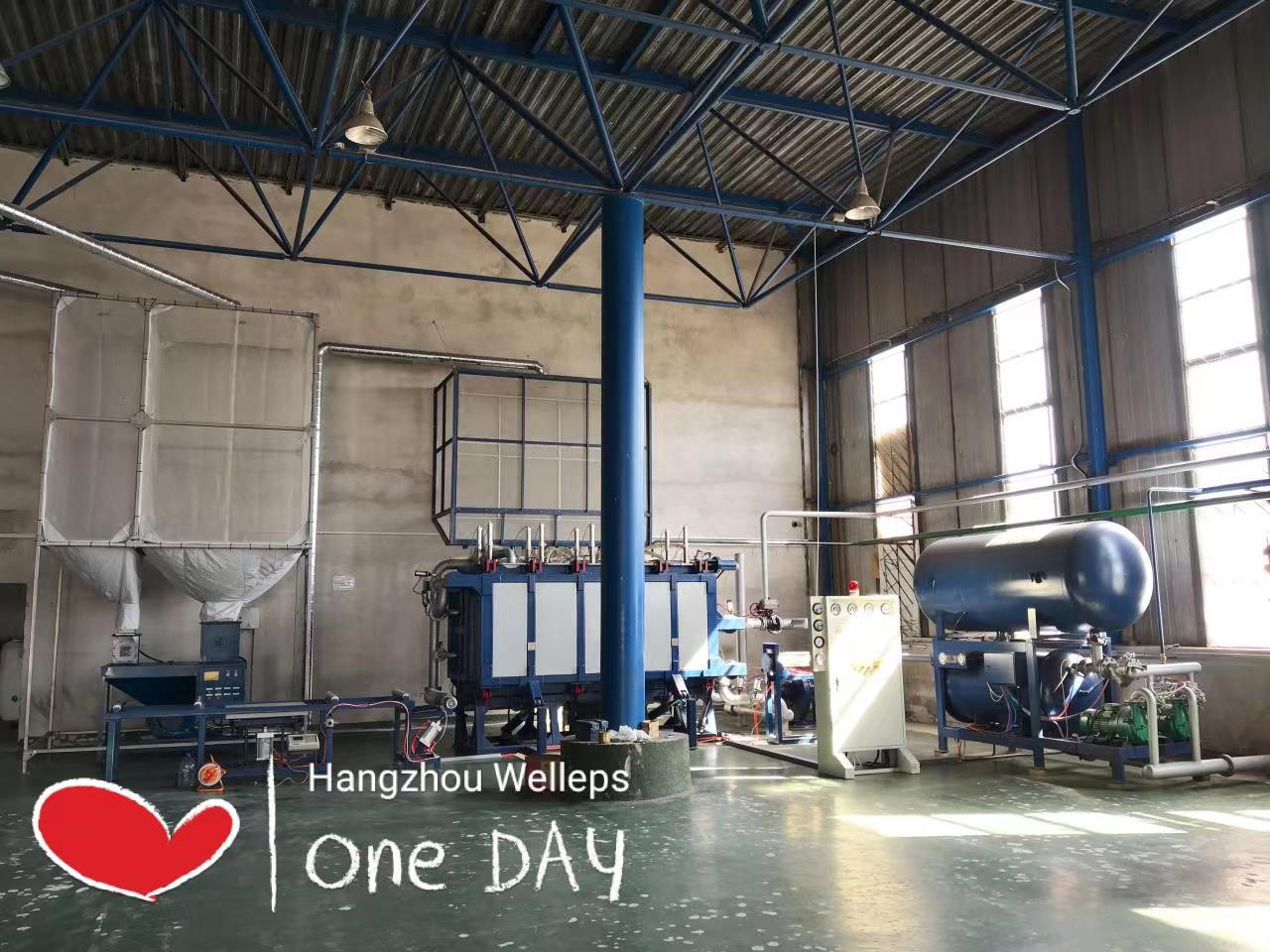
2. Mold closing: The automatic sheet metal factory reminds everyone to open the mold before closing. 1) Mold opening: Mold opening, with all drain valves and drain valves open. The top rod retracts from the pushed out position to its original state and pauses for a few seconds. 2) Mold closing: In general, the mold closing process changes from fast to slow to prevent mold collisions. The conversion of mold closing speed is usually achieved by controlling the conversion of the oil circuit through a travel switch.
3. Mold filling: 1) Feeding, including intermittent feeding and non intermittent feeding. If vacuum feeding is used, uninterrupted feeding can be used directly, but at this point, the exhaust valve and exhaust valve need to be closed, and the vacuum valve needs to be opened. 2) After returning the material, the mold cavity is filled with material, and compressed air must be blown out through the feed pipe and hopper. In this way, the remaining material in the material pipe is blown back into the hopper to avoid sticking and blocking the remaining material in the material pipe during the heating process. 3) Turn off the material gun, turn off and lock the material gun, and stop the gas supply.
4. Heating: The automatic sheet metal factory reminds everyone that in order to obtain products with uniform and complete fusion, uniform heating is necessary. The conductive heating method with a wall thickness not exceeding 2 or 4cm can be used for manufacturing parts. But when the wall thickness exceeds this limit, the result of using conduction heating method may cause the surface of the workpiece to seal prematurely before complete internal fusion.
5. Cooling: Common cooling methods include water cooling and vacuum cooling. By cooling with water, the surface of the product can be smooth and the strength of the product can be increased. The vacuum cooling time is generally short. The automatic sheet metal factory reminds everyone that the cooling time should be tested according to different molds. If the time is too short, bead protrusions may appear on the surface of the product, and sometimes thick walled products may even crack; The time is too long, which prolongs the cycle and reduces work efficiency.
6. Demolding: Use compressed air to blow the product onto one side of the fixed mold to ensure smooth demolding of the product. The automatic sheet metal factory reminds everyone to use compressed air to assist in demolding after opening the mold stroke, and then use a mechanical ejector rod to push the product out of the mold.
Post time: Apr-27-2023