EPS Floor Heating Plate moulding Machine
Main Features
EPS Floor Heating Plate produced by EPS Floor Heating Plate moulding Machine has the features of light weight, low thermal conductivity, low water absorption, anti-vibration, anti-impact, sound insulation, shockproof, heat insulation and moisture proof. Therefore, it is the most practical and cost-effective thermal insulation material to use EPS plastic as thermal insulation in the underfloor heating system.
1. Polystyrene plastic is suitable for use at lower temperatures because EPS underfloor heating panels are made from polystyrene foam particles, which have a softening temperature of only about 88°C, and a practical maximum operating temperature of only about 75°C. The main drawback is that it is not temperature-resistant, but the water supply for underfloor heating is limited to a temperature of no more than 60°C, so there is no impact on the overall stability and strength of the underfloor heating system structure.
2.The lower the density of EPS floor heating board, the lower its thermal conductivity. When the density drops to 32kg/m3, the thermal conductivity reaches its lowest point, which leads to a further drop in density. Therefore, from the point of view of thermal insulation, thermal insulation panels for underfloor heating make sense. a density of 32 kg/m3 is ideal.
3. Compressive strength has a strong inverse relationship with its density; compressive strength decreases with density and vice versa.
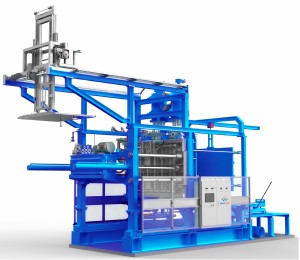
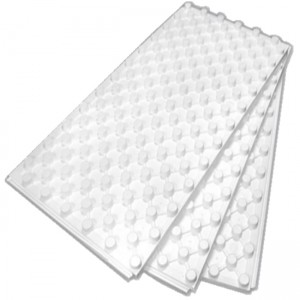
Technical Data
Item | Unit | Type | ||||||
PSZ100JN | PSZ120JN | PSZ140JN | PSZ160JN | PSZ175JN | PSZ180JN | |||
Mould Dimension | mm | mm | 1000*800 | 1200*1000 | 1400*1200 | 1600*1350 | 1750*1450 | 1800*1600 |
Max Product Dimension | mm | mm | 800*600
*330 |
1000*800
*330 |
1200*1000
*330 |
1400*1100
*330 |
1550*1200
*330 |
1610*1400
*330 |
Stroke | mm | 190-1400 | 190-1400 | 190-1400 | 210-1410 | 210-1410 | 210-1410 | |
Steam | Entry | mm | DN65 | DN65 | DN10 | DN100 | DN100 | DN100 |
Consumption | kg/cycle | (8-10T)Steam of 1T material 每吨原料消耗8-10吨蒸汽 | ||||||
Cooling Water | Entry | mm | DN65 | DN65 | DN65 | DN65 | DN65 | DN65 |
Consumption | kg/cycle | 40-120 | 40-138 | 50-150 | 55-180 | 60-190 | 80-200 | |
Compressed Air | Entry | mm | DN40 | DN40 | DN40 | DN50 | DN50 | DN50 |
Consumption | m3/cycle | 1.2 | 1.2 | 1.2 | 1.4 | 1.5 | 1.5 | |
Vacuum Pump Capacity | m3/h | 165 | 165 | 230 | 280 | 280 | 280 | |
Power | Kw | 11 | 11 | 12.5 | 16.5 | 16.5 | 16.5 | |
Overall Dimension | L*W*H | mm | 4500*1640
*2700 |
4500*1840
*2900 |
4600*2140
*3100 |
5000*2300
*3100 |
5000*2450
*3500 |
5000*2610
*3800 |
Weight | kg | 4500 | 5200 | 5700 | 7000 | 7500 | 8000 | |
Cycle Time | s | 60-90 | 60-100 | 60-120 | 70-130 | 70-130 | 80-140 |